DRYLUFT
HLR

HEATLESS REGENERATION ADSORPTION DRYERS
The heat less regeneration adsorption dryer is based on pressure swing adsorption. When the water vapor in the mixed component is high partial pressure, the adsorbent adsorbs moisture, and in the low partial pressure of water vapor environment, the adsorbed moisture in the adsorbent is completed. Desorption” and return to the gas phase, the adsorbent thus obtains active regeneration. The low partial pressure desorption air used in the heat less regeneration dryer is taken from part of the product gas output by this machine. The regeneration gas and the product gas are homologous to the heat less regeneration adsorption dryer, which brings great convenience to the structure. Simple, the operation process is also very convenient. In the heat less regeneration process, the desorbed gas is not only the energy necessary for regeneration, but also serves as a truncated body for water vapor discharge. Since pressure swing adsorption is generally regarded as an isothermal process, the heat less regeneration dryer does not need to be equipped with a cooling process. The desorption and regeneration of the adsorbent are completed simultaneously in the heat less regeneration.
DESIGN FEATURES:
- Using high-performance pneumatic valve, reliable performance, sensitive action, fast and reliable switching and long life.
- Using high-torque aluminum alloy pneumatic actuator, with large torque and stable action
- Using high-efficiency adsorbent with large specific surface area, strong adsorption capacity and strong wear resistance, to ensure that the dew point is stable for long-term use and he adsorbent does not powder.
- Using a fully electronic programmable controller, easy to understand, easy to operate and maintain
- Low operating noise, using a silent one-way valve and high-performance muffler to ensure that the noise is reduced to a minimum during the entire operation and exhaust process.
- Automatic stamping function, automatic stamping before valve switching, so that the cylinder pressure is equalized and then switched to ensure the stability of the cylinder pressure, avoid the impact of pipeline pressure fluctuation on the adsorbent, and ensure the longevity of the adsorbent.
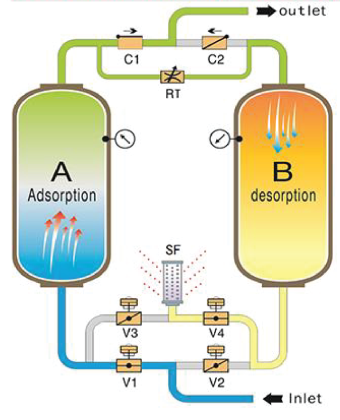
RELIABLE ACCESSORIES :
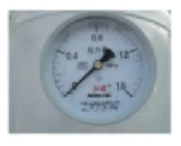
MC CERTIFIED PRESSURE GAUGE
Adopting HONGQI pressure gauge certified by national MC measurement
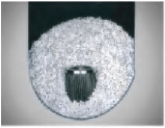
GAS DIFFUSION DEVICE
The stainless steel increased flow design ensures that the air flow evenly passes through the adsorption tower to achieve the highest adsorption efficiency
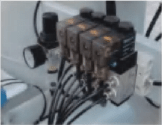
PNEUMATIC CONTROL COMPONENTS
The operating life can reach 1million times which ensure the life for unit in operation for 5 to 10 years
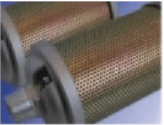
IMPORTED SILENCER
Adopting HONGQI pressure gauge certified by national MC measurement
DRYLUFT
HLR
HEATLESS REGENERATION ADSORPTION DRYER

Heatless regeneration adsorption dryer is a conventional series of products of Reinigen company, which is positioned as stable and durable. Compared with freeze dryer, it can achieve lower dew point, but it will consume a part of compressed air. The design has simple structure and low failure rate.
OPERATING CONDITIONS AND TECHNICAL REQUIREMENTS:
- Rated air inlet pressure : 0.7MPa (0.6MPa ~ 1.0MPa allowed)
- Rated inlet air temperature : 10 °C~ 30 °C(2 °C ~ 40°C is allowed)
- Atmospheric dew point of finished gas: -40°C ~ 40°C
- Ambient temperature : ≤ 45°C
- Pressure loss: <_ 0.02MPa
- Regeneration mode: heatless regeneration
- Adsorbent: activated alumina + high efficiency molecular sieve
- Oil content of intake air: ≤ 0.02MPa
- Average regeneration gas consumption: 8-14% gas consumption
- Control mode: full electronic programmable time control (dew point control optional)
WORKING PRINCIPLE:
The heatless regeneration dryer uses the PSA pressure swing adsorption principle, the regeneration process is not heated, and the compressed air is dried through the double tower circulation adsorption process. One adsorption tower absorbs the water in the compressed air under a certain pressure, the other uses a small part of the dried air to reduce the pressure for regeneration, and after a certain time, the two towers switch to each other, so as to realize the continuous adsorption and purification of air.
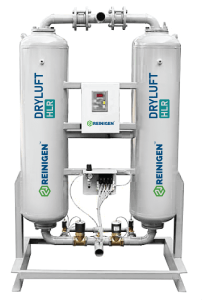
TECHNICAL DATA SHEET OF DRYLUFT HLR HEATLESS REGENERATION ADSORPTION DRYER
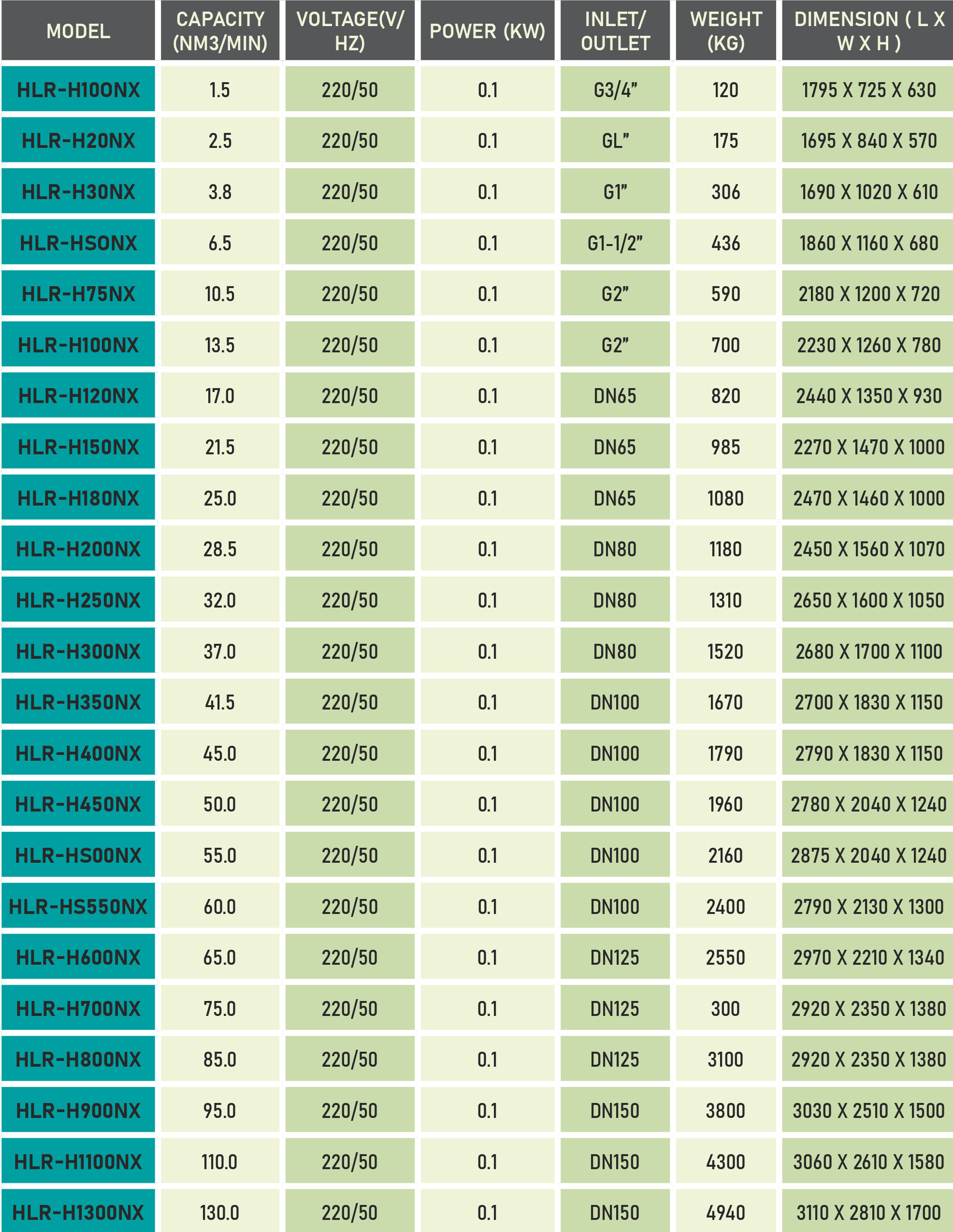
* Note: the above data is for reference, contact us for detailed technical parameters.
DRYLUFT
MHR

MICRO HEAT REGENERATED ADSORPTION DRYERS
The micro-heat regeneration adsorption dryer works according to the principle of temperature swing adsorption, that is, the adsorbent absorbs moisture at room temperature, and the moisture adsorbed by the adsorbent completes “desorption” at high temperature and returns to the gas phase. In this process, an external heat source provides the heat required for desorption, and uses part of this product gas a heat carrier. In the adsorbent regeneration process, all the adsorbed water returns to the gas phase, which
does not mean that the adsorbent regeneration has been completed. The original adsorption activity is fully restored when the temperature is lowered to the initial value. Therefore, the regeneration process of the micro-heat regeneration adsorption dryer must be carried out in two steps, that is, “heating and desorption” first, and then “cooling and regeneration” ; “ desorption” is only one step of adsorbent regeneration.
DESIGN FEATURES:
- Using high-performance pneumatic valve, reliable performance, sensitive action, rapid switching, reliable and long life.
- Using high-torque aluminium alloy pneumatic actuator, with large torque and stable action.
- Using high-efficiency adsorbent with large specific surface area and strong adsorption capacity. Strong abrasion resistance, to ensure that the dew point is stable and does not powder after long-tem use.
- Using a fully electronic programmable controller, Chinese interface, easy to install, easy to operate and maintain.
- Low operating noise, using a silent one-way valve and high-performance muffler to ensure that the noise is reduced to a minimum during the entire operation an exhaust process.
- Automatic stamping function, automatic stamping before the valve switch, so that the cylinder pressure is equalized and then switched to ensure the stability of the cylinder pressure, avoid the impact of pipeline pressure fluctuation on the adsorbent, and ensure the service life of the adsorbent.
- The heater is equipped with pressure protection to prevent the heater from burning dry and improve the service life of the heater.
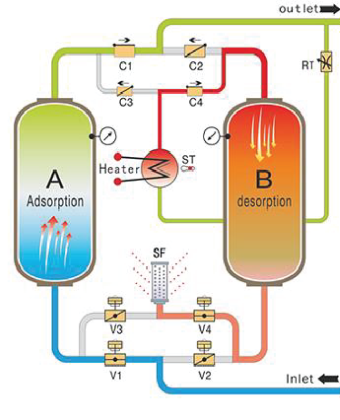
RELIABLE ACCESSORIES :
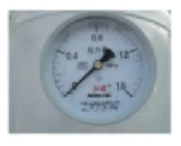
EXTERNAL HIGH EFFICIENCY HEATER
Highly intensive compact structure, imported alloy heating element, 316 stainless steel seamless pipe body, good mechanical performance under high pressure gas impact.
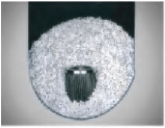
IMPORTED PNEUMATIC BUTTERFLY VALVE
Adopt Germen imported pneumatic butterfly valve for precise integration, after rigorous calculation, the scaling ring and the media plate have no friction, and the operating life is up to 2 million times
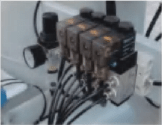
MICROCOMPUTER CONTROL SYSTEM
Use single-chip microcomputer control mode to implant mature control program to automatically control the operation of the unit, multiple modes and function options.
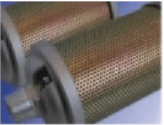
GNH-280 MOLECULAR MEMBERSHIP
GNH-280 has high-efficiency adsorption performance and high-strength abrasion resistance, and the adsorption heat reaches 4200 dry coke, Long service life, reducing operating costs in actual use.
DRYLUFT
MHR

MICRO HEAT REGENERATED ADSORPTION DRYERS
Micro-heat regeneration adsorption dryer is a conventional series of products of Reinigen company, which is positioned as stable and durable. One the basis of heatless regeneration adsorption dryer, it added regeneration gas heater, which has better energy-saving type compared with heatless regeneration adsorption dryer.
OPERATING CONDITIONS AND TECHNICAL REQUIREMENTS:
- Rated air inlet pressure: 0.7MPa (0.6MPa ~ 1.0MPa allowed)
- Rated inlet air temperature: 10 °C ~ 30 °C (2 °C ~ 40 °C is allowed)
- Atmospheric dew point of finished gas: – 40 °C (customized below -40 °C)
- Ambient temperature: ≤ 45 °C
- Pressure loss: ≤0.02MPa
- Regeneration mode: heating regeneration
- Adsorbent: activated alumina + high efficiency molecular sieve
- Oil content of intake air: ≤ 0.1mg/m*
- Average regeneration gas consumption: 4-8% gas consumption
- Control mode: full electronic programmable time control (dew point control optional)
WORKING PRINCIPLE:
The heated regeneration adsorption dryer makes full use of the characteristics of adsorbent (adsorption under high pressure and low temperature, desorption under low pressure and high temperature) and improves the adsorption capacity of adsorbent within unit mass, so as to achieve the purpose of deep drying of compressed air. It has the advantages of simple structure, high degree of automation, less gas consumption and deep desorption of PSA adsorption dryer. It can avoid the weakness of large gas consumption and frequent switching of the heatless regeneration dryer. Its comprehensive index has obvious advantages and more energy consumption saving, thus effectively reducing the user’s use cost.
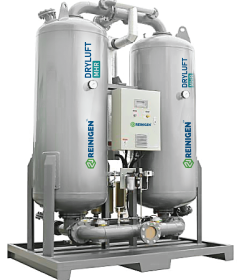
TECHNICAL DATA SHEET OF DRYLUFT MHR MICRO-HEAT REGENERATION ADSORPTION DRYER
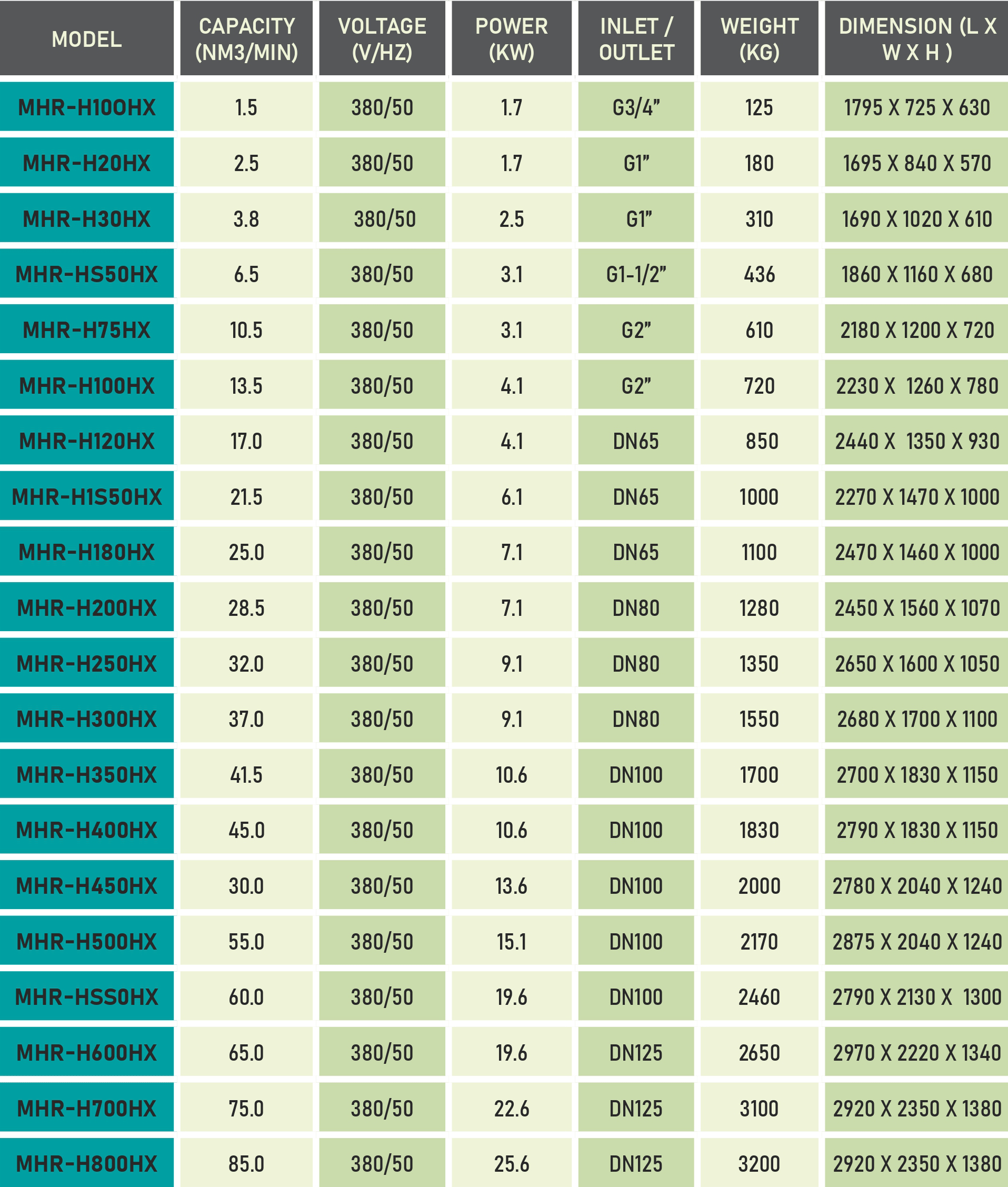
* Note: the above data is for reference, contact us for detailed technical parameters.
DRYLUFT
CTD

COMPRESSED AIR COMBINATION TYPE DRYER
The high-temperature and high-humidity compressed air from the compressor first exchanges heat with the dried low-temperature compressed air in the heat exchanger of the refrigeration dryer to reduce the temperature, and then enters the evaporator to be further cooled. Most of the gaseous water in the evaporator. The molecules condense into liquid water and are discharged. After that, the compressed air with very low moisture content enters the adsorption cylinder to be further dried and dehumidified to
obtain a product gas with as lower dew point. Finally the low-temperature dry compressed air enters the heat exchanger to cool the high-temperature and high-humidity inlet air, and at the same time, its temperature rises. High to prevent condensation outside the conveying pipeline, a small part of the dry compressed air after the temperature is used for the regeneration of the adsorbent, which improves the regeneration efficiency and reduces energy consumption.
DESIGN FEATURES:
- Energy saving in every aspect
The unique process design, the adsorption system adsorbs at low temperature and regenerates at room temperature, to ensure that the loss of compressed air during regeneration is minimized, and the power consumption of the refrigeration system can reduced by 2040%. Effectively improve the efficiency of the air compressor, the entire air compressor system exerts its own advantages to operate in the best condition to achieve the highest service life, which benefits from its design scheme and advanced technology.
- The best built-in precision filter design
The built-in high-efficiency precision filter fully filters impurities such as oil vapor contained in the compressed air at a low temperature of 2~5°C Filtering at low temperature makes the precision filter play the greatest filtering effect the filter efficiency is increased by more than 50% which fully improves the service life of the filter, and more effectively prevents the adsorption system form being polluted.
- Advanced refrigeration drying system and adsorption drying system design
The design of the refrigeration drying system is advanced, the contact area between compressed air and Freon is large, the time is long, and the heat exchange is more thorough. Imported high-precision refrigeration components, advanced expansion throttling devices and the temperature automatic capacity adjustment device automatically adjust to the best state according to the changing working conditions effectively reducing the electric energy consumption of the refrigeration compressor and further saving energy consumption. The best adsorption cycle of the adsorption drying system uses highly efficient adsorbents, which have high strength and absorption resistance, and have better adsorption efficiency. The best solution is to adsorb water at low temperatures. Extremely increase the adsorption depth and obtain extremely low dew point.
- Durable and user-friendly design
The integrated design makes it more sophisticated, small footprint and easy to install; years of research and technology have been successfully produced with modern technology and equipment, and every product is strictly controlled. It is allowed to leave the factory only if the standard test meets the usage standard, to ensure that you are satisfied from stat to finish.
DRYLUFT
CTD

COMPRESSED AIR COMBINATION TYPE DRYER
CTD series combined dryer combines the advantages of freeze dryer and adsorption dryer. Through unique design, the two are skid connected. Through the treatment of combined dryer, it can reach a very low pressure dew point.
OPERATING CONDITIONS AND TECHNICAL REQUIREMENTS:
- Rated air inlet pressure: 0./MPa (0.6-1.Ompa is allowed to be used, other working pressures are customized)
- Rated air inlet temperature: 50 °C (≤ 80 °C allowed)
- Outlet pressure dew point: ≤ 40 °C (other pressure dew points are required to be customized)
- Rated ambient temperature: ≤ 45 °C
- Pressure loss: ≤ 0.047MPa
- Average regeneration gas consumption: 3%-5% (micro-heat); 4%-6%(heatless)
- Regeneration mode: micro-heat/ heatless regeneration
- Adsorbent: activated alumina + high efficiency molecular sieve
- Oil content of intake air: ≤ 0.4mg/m*
- Cooling mode: air cooling/ water cooling
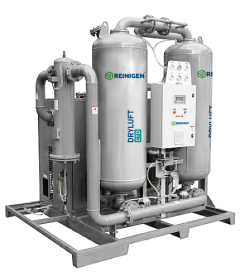
OPERATING CONDITIONS AND TECHNICAL REQUIREMENTS:
The humid air first enters the pre-cooler in the freezer drying system and exchanges heat with the dry low dew point air from the adsorption drying system, which increases the temperature of the low dew point air and reduces the intake air the temperature of the compressed air entering the evaporator removes a part of the water and lowers it to room temperature, reducing the work load of the evaporator. Then enter the evaporator for heat exchange to cool the compressed air to around the dew point temperature most of the water, oil and some impurities in the compressed air are condensed here, and the air and water are fully separated by the air-water separator. The pressure after preliminary drying the compressed air enters the adsorption drying system through the degreasing filter. The air is deeply absorbed by the high-efficiency molecular sieve in the adsorption bed, and finally compressed air with low dew point is obtained. Low dew point pressure the compressed air than passes through a precision filter to remove dust, and finally gets ultra-low dew point and clean compressed air.
TECHNICAL DATA SHEET OF DRYLUFT CTD COMPRESSED AIR COMBINATION TYPE DRYER
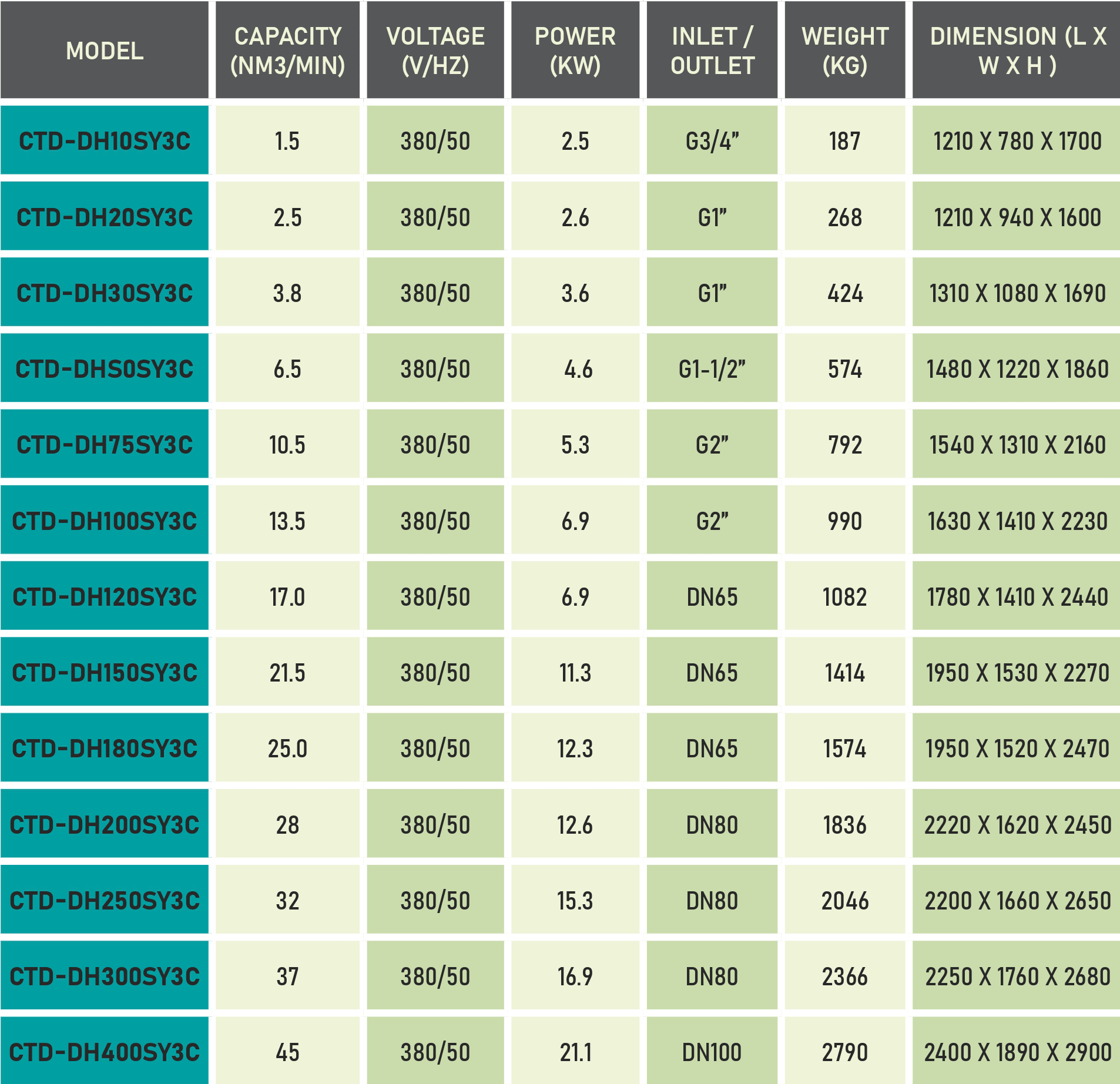
* Note: the above data is for reference, contact us for detailed technical parameters
DRYLUFT
HRB – Z

BLOWER HEAT REGENERATION ADSORPTION DRYER (ZERO LOSS)
HRB-Z series blower heat gas consumption regenerative adsorption dryer of Reinigen company adds blower circulation system on the basis to traditional micro heat regeneration adsorption dryer. Through the precise control of PLC and the cooperation of each group of valves, the regeneration process of adsorbent dose not consume compressed air of finished products, so as to achieve zero gas consumption in the regeneration process and achieve the purpose of energy saving.
OPERATING CONDITIONS AND TECHNICAL REQUIREMENTS:
- Rated air inlet pressure: 0.7MPa (0.6-1.0mpa is allowed to be used, other working pressures are customized)
- Rated air inlet temperature: 30 °C (2 °C – 40 °C allowed)
- Outlet pressure dew point: ≤ – 20 °C, ≤ – 40 °C (other pressure dew points are required to be customized) • Rated ambient temperature: 35 °C (2 °C – 40 °C allowed)
- Cooling water pressure: 2bar-6bar
- Cooling water temperature: 25 °C (2 °C – 32 °C is allowed to use)
- Pressure loss: ≤ 0.02MPa
- Oil content of intake air: ≤ 0.1ppm
- Average regeneration gas consumption: ≈ 0%
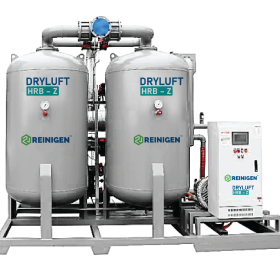
WORKING PRINCIPLE:
The blower heat regenerative adsorption dryer (Zero gas loss) is composed of two adsorption towers which work alternately, including blower, electric heater system, cooler system, switching valve system, control system, etc. The zero air consumption regenerative adsorption dryer with air blast heat is based on the micro air consumption heated by the heater to desorb the moisture form the adsorbent. In the cooling stage, the hot air circulates through the cooler and the regeneration tower. The regeneration tower is cooled and desorbed by continuous closed cycle. The whole regeneration process does not consume compressed air
TECHNICAL DATA SHEET OF DRYLUFT HRB-Z -BLOWER HEAT REGENERATION ADSORPTION DRYER (ZERO LOSS)
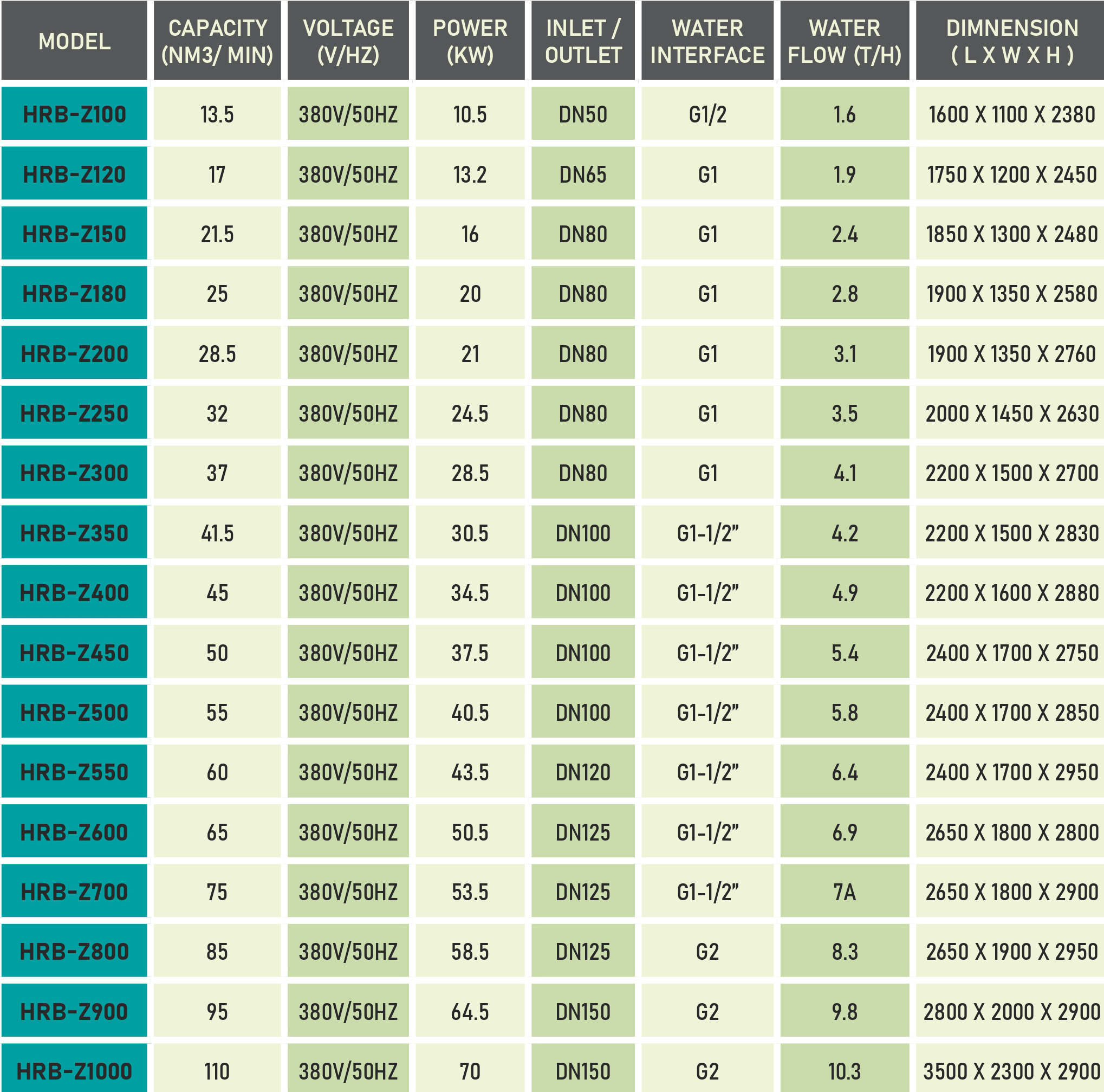
* Note: the above data is for reference, contact us for detailed technical parameters.
DRYLUFT
HRB – E

BLOWER HEAT REGENERATION ADSORPTION DRYER (MICRO LOSS)
HRB-E series blower heated micro gas consumption regenerative adsorption dryer of Reinigen company adds blower circulation system on the basis of traditional micro heat regeneration adsorption dryer, so that only a small amount of finished compressed air is consumed in the cooling process when the adsorbent is regenerated. It greatly reduces the consumption of compressed air in the regeneration process of adsorbent and achieves the purpose of energy saving.
OPERATING CONDITIONS AND TECHNICAL REQUIREMENTS:
- Rated air inlet pressure: 0.7MPa (0.6-1.0MPa is allowed to be used, other working pressures are customized)
- Rated air inlet temperature: 30°C ( 2°C – 40°C allowed)
- Outlet pressure dew point: ≤ – 20°C, ≤ – 40°C ( other pressure dew points are required to be customized)
- Rated ambient temperature : 35°C ( 2°C – 40°C allowed)
- Pressure loss : ≤ 0.02MPa
- Oil content of intake air: ≤ 0.1ppm
- Average regeneration gas consumption: ≤ 2%
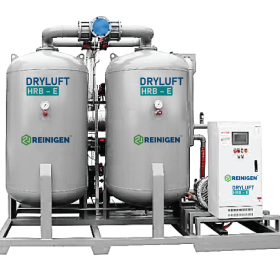
WORKING PRINCIPLE:
The blower heated regenerative adsorption dryer (Micro gas consumption) is composed to two adsorption towers which work alternately, including blower, electric heater system, switching valve system, control system, etc. in the whole working cycle, one adsorption tower is in adsorption, the other adsorption tower is in regeneration desorption. On the basis of the micro heat regeneration adsorption dryer, an independent high-efficiency blower is added. The ambient air inhaled by the blower is heated by the heater to desorb the moisture from the adsorbent in the cooling stage, about 2% of the finished gas is used as the regeneration gas. The whole regeneration process consumes very little compressed air.
TECHNICAL DATA SHEET OF DRYLUFT HRB-E BLOWER HEAT REGENERATION ADSORPTION DRYER (MICRO LOSS)
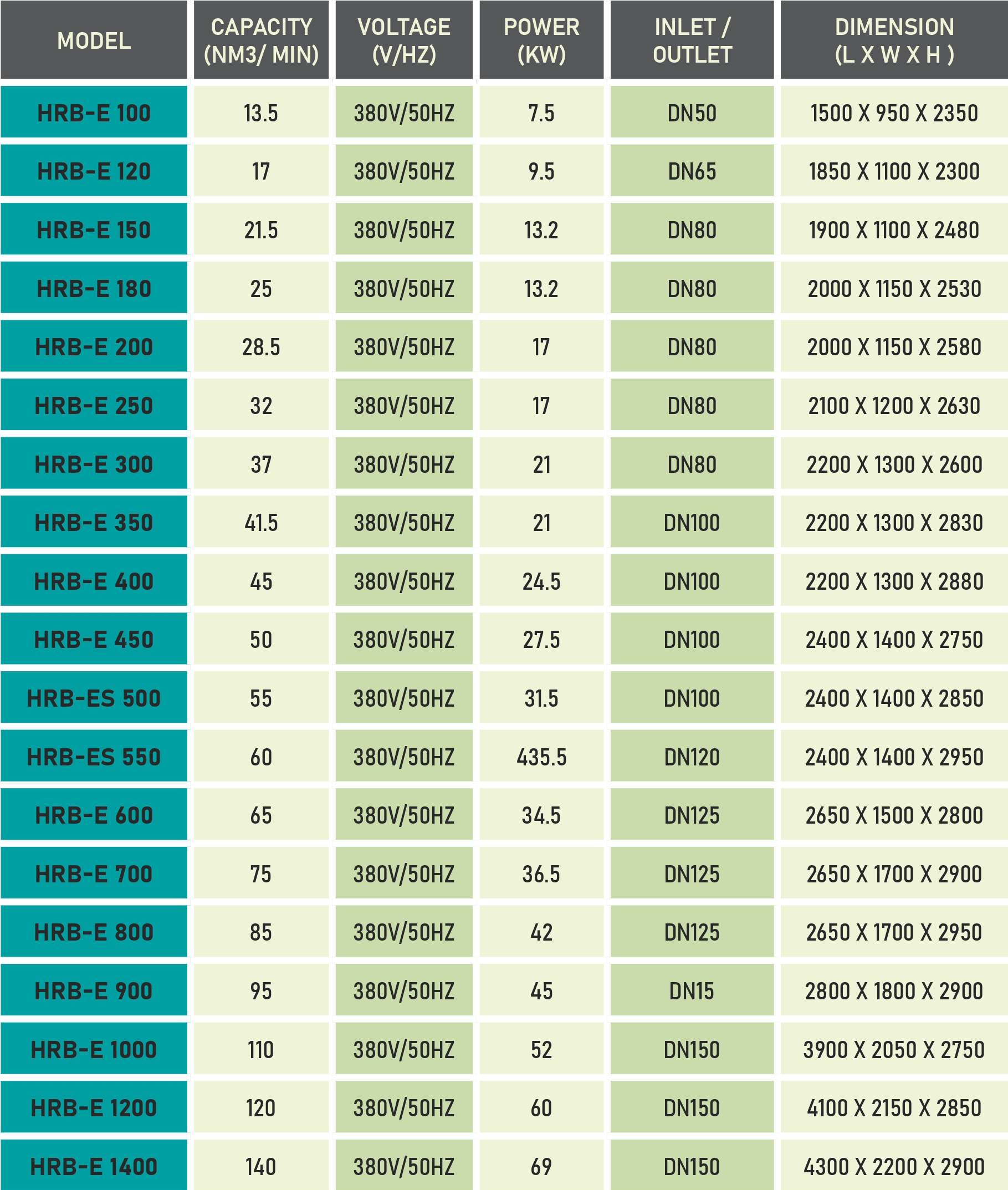
* Note: the above data is for reference, contact us for detailed technical parameters.
DRYLUFT
HOC –Z

COMPRESSION HEAT REGENERATION ADSORPTION DRYER (ZERO LOSS)
HOZ- Z series waste heat zero gas consumption regenerative adsorption dryer is developed by Reinigen company for centrifugal air compressor of oil-free air compressor and other models with high exhaust temperature and no oil. This series of products no longer rely on additional heaters, but only make full use of the waste heat generated by air compression process to regenerate the adsorbent. Thus “Zero energy consumption” and zero gas consumption can be realized in the regeneration process.
OPERATING CONDITIONS AND TECHNICAL REQUIREMENTS:
- Rated air inlet pressure: 0.7MPa (0.6-1.0mpa is allowed to be used, other working pressures are customized)
- Rated air inlet temperature: 125 °C (110 °C – 140 °C allowed)
- Outlet pressure dew point: ≤ – 20 °C, ≤ – 40 ‘C (other pressure dew points are required to be customized)
- Rated ambient temperature: 35 °C (2 °C – 40 °C allowed)
- Cooling water pressure: 2bar-6bar
- Cooling water temperature: 25 °C (2 °C – 32 °C is allowed to use)
- Pressure loss: ≤ 0.035MPa
- Oil content of intake air: Oil free air
- Average regeneration gas consumption: ≈ 0%
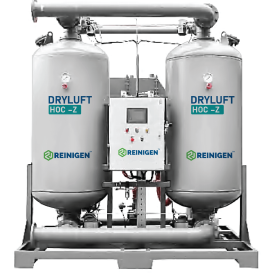
WORKING PRINCIPLE:
The working principle of the zero gas consumption waste heat regeneration dryer is to use the heat of the high temperature air discharged by the air compressor to directly heat up the adsorbent after the adsorption process, so that the adsorbent can be completely dehydrated and regenerated. Because there is no gas consumption during the heating regeneration process, the energy is saved to maximum extent. The zero gas consumption compression heat adsorption dryer is based on the ordinary compression heat adsorption dryer, adding auxiliary high-efficiency cooler and related components, to achieve the complete zero gas consumption.
TECHNICAL DATA SHEET OF DRYLUFT HOC –Z COMPRESSION HEAT REGENERATION ADSORPTION DRYER (ZERO LOSS)
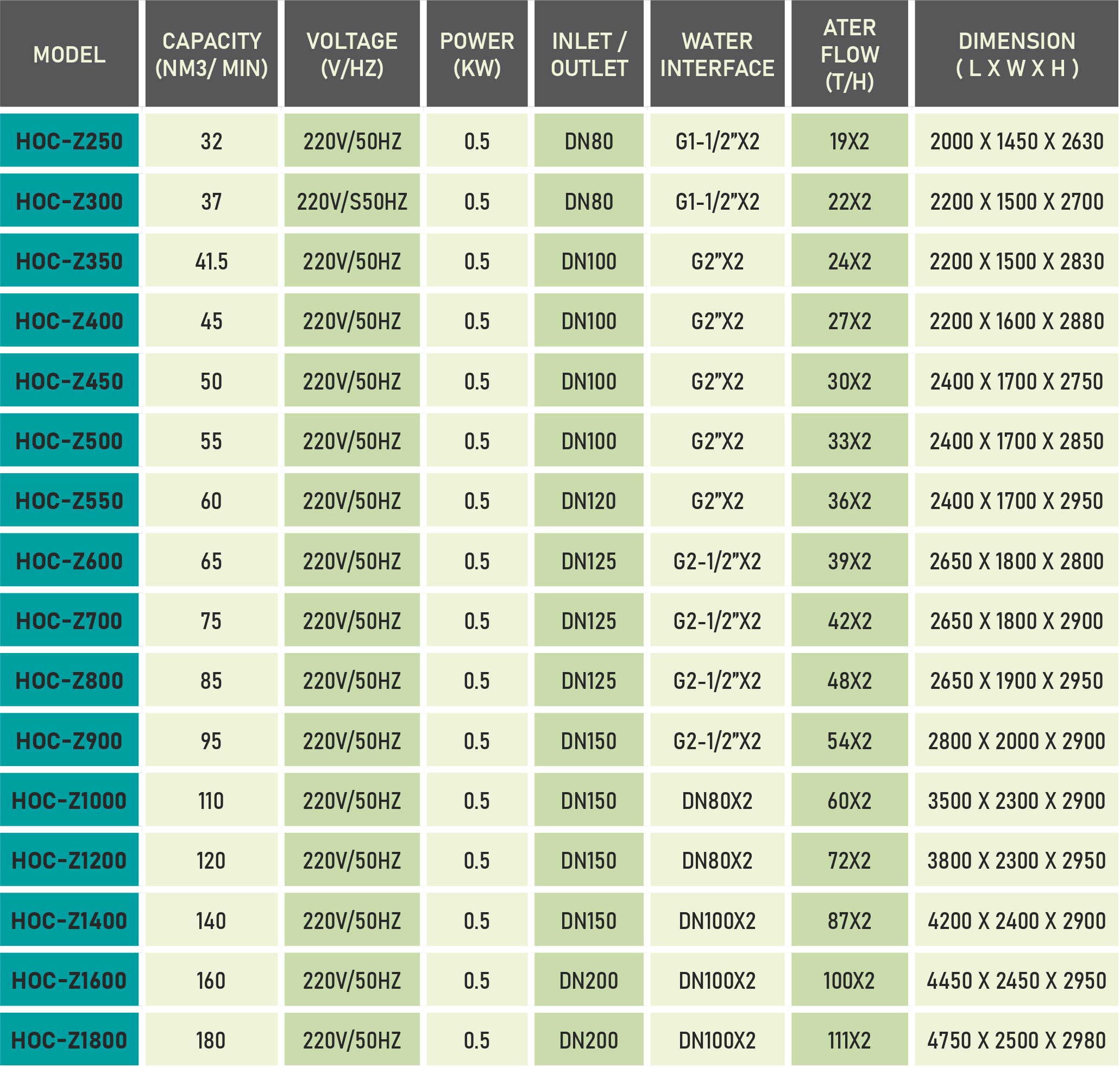
* Note: the above data is for reference, contact us for detailed technical parameters, if the inlet temperature of the dryer is lower than 110 °C or the pressure dew point is required to be lower than - 40 ‘C, the auxiliary heating system shall be added.
DRYLUFT
HOC – E

COMPRESSION HEAT REGENERATION ADSORPTION DRYER (MICRO LOSS)
HOC-E series waste heat micro gas consumption regenerative adsorption dryer is developed by Reingen company for centrifugal air compressor or oil-free air compressor and other models with high exhaust temperature and no oil. This series of products no longer rely on additional heaters, and make full use of the waste heat generated in the air compression process to regenerate the adsorbent, only consumed in the cooling process a small amount of finished compressed air.
OPERATING CONDITIONS AND TECHNICAL REQUIREMENTS:
- Rated air inlet pressure: 0.7/MPa (0.6-1.0mpa is allowed to be used, other working pressures are customized)
- Rated air inlet temperature: 125 °C (110 °C – 140 °C allowed)
- Outlet pressure dew point: ≤ – 20 °C, ≤ – 40 C (other pressure dew points are required to be customized)
- Rated ambient temperature: 35 °C (2 °C – 40 °C allowed)
- Cooling water pressure: 2bar-6bar
- Cooling water temperature: 25 °C (2 °C – 32 °C is allowed to use)
- Pressure loss: ≤ 0.035MPa
- Oil content of intake air: Oil free air
- Average regeneration gas consumption: ≈ 2% – 3%
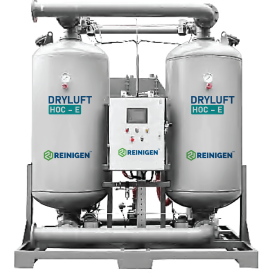
WORKING PRINCIPLE:
The working principle of the micro gas waste heat regeneration dryer is to use the heat of the high temperature air discharged from the air compressor to directly heat the adsorbent after the adsorption process, so that the adsorbent can be completely dehydrated and regenerated. In the process of heating and regeneration, compressed air is not consumed, only a small amount of compressed air (2% – 3%) is used in the cooling stage, which greatly saves energy. Its unique design, fuzzy cycle logic, perfect temperature control and alarm functions ensure the complete regeneration of adsorbent, and solve the problems such as ordinary compression type heat dryer can not adapt to the change of working conditions, gas volume change, adsorbent bubble water powder crushing and so on.
TECHNICAL DATA SHEET OF DRYLUFT HOC-E COMPRESSION HEAT REGENERATION ADSORPTION DRYER (MICRO LOSS)
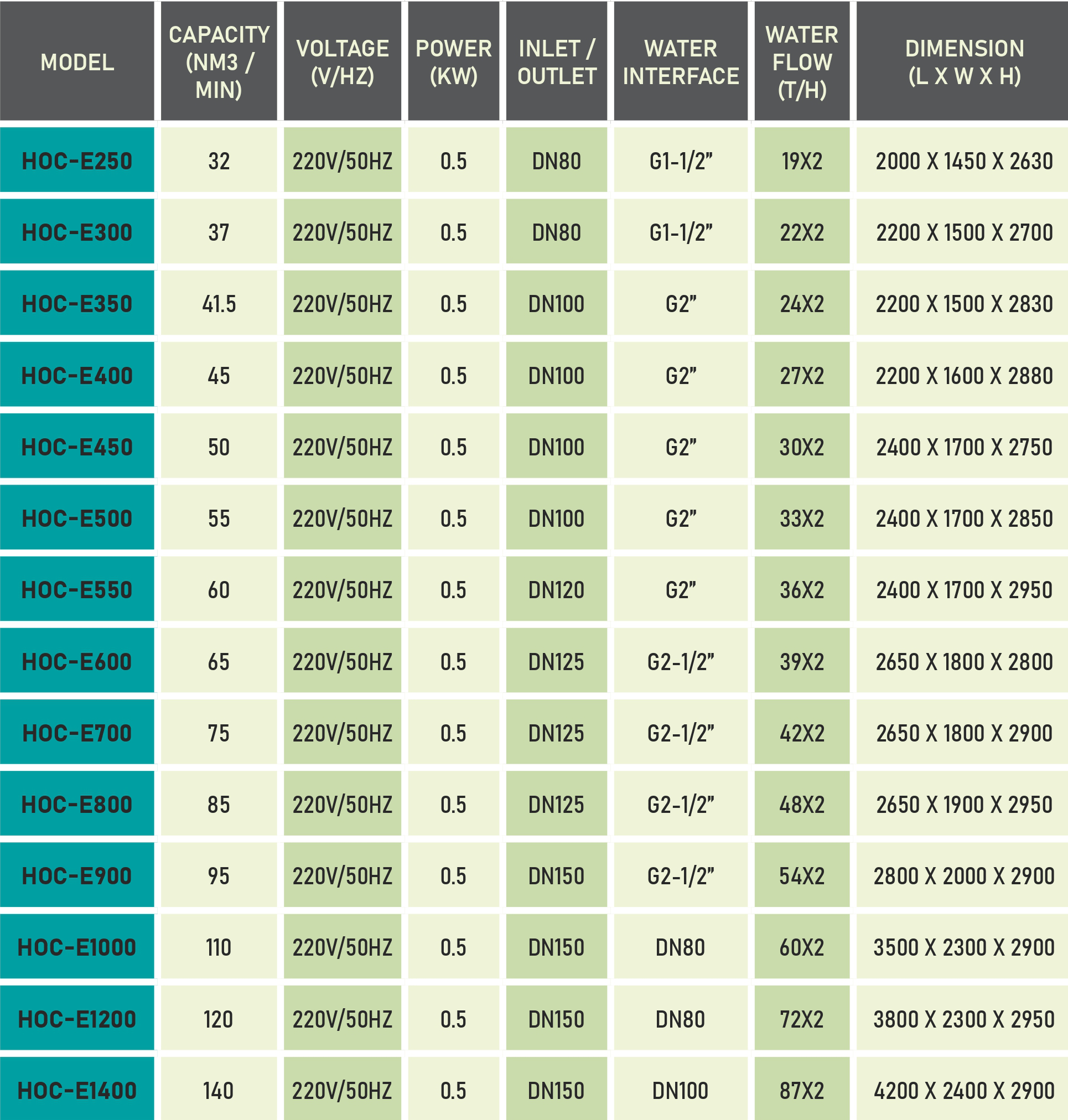
Note: the above data is for reference, contact us for detailed technical parameters, if the inlet temperature of the dryer is lower than 110 °C or the pressure dew point is required to be lower than - 40 °C, the auxiliary heating system shall be added.
DRYLUFT
MAD

MODULAR ADSORPTION DRYER
DRYLUFT MAD-series modular adsorption dryer is a high value-added product newly developed by Reinigen company. Compared with the traditional dryer, this series of products are smaller and smaller. 13X molecular sieve and straight through adsorption chamber make the adsorbent more efficient. At the same time, the whole machine is mainly made of high-quality aluminium alloy, which avoids secondary pollution to the compressed air.
OPERATING CONDITIONS AND TECHNICAL REQUIREMENTS:
- Rated air inlet pressure: 0.7MPa (0.6-1.0mpa is allowed to be used, other working pressures are customized)
- Rated air inlet temperature: 10-30 °C (2-40 °C allowed)
- Inlet air dew point: ≤15 °C
- Outlet air dew point: ≤ – 40 °C (other pressure dew points are required to be customized)
- Rated ambient temperature: 35 °C (2 °C – 45 °C allowed)
- Working principle: PSA pressure swing adsorption and self-heating regeneration
- Inlet air oil content requirement: No oil or ≤ 0.1ppm (mg/m3)
- Pressure loss: ≤ 0.02MPa
- Average regeneration gas consumption: ≈ 13.5%-14.5%
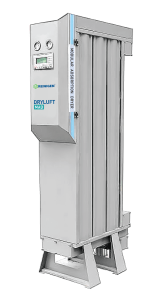
WORKING PRINCIPLE:
DRYLUFT MAD series adsorption dryer adopts non thermal method (PSA) to regenerate adsorption materials. This is the simplest type of adsorption and has long been the choice of many industries and applications. For small and medium-sized flow systems, these technologies are usually the only feasible technologies. The modular design makes the M series a more reliable, smaller, more compact and lightweight solution. They can be installed in the compressor room or at the point of use. Compared with the traditional double tower dryer design, the modular structure is usually smaller and lighter than the similar twin tower dryer. Provide an easy to install and easy to maintain design, completely corrosion-resistant, better suitable for medical, food, electronic and other industries.
TECHNICAL DATA SHEET OF DRYLUFT -MAD- MODULAR ADSORPTION DRYER
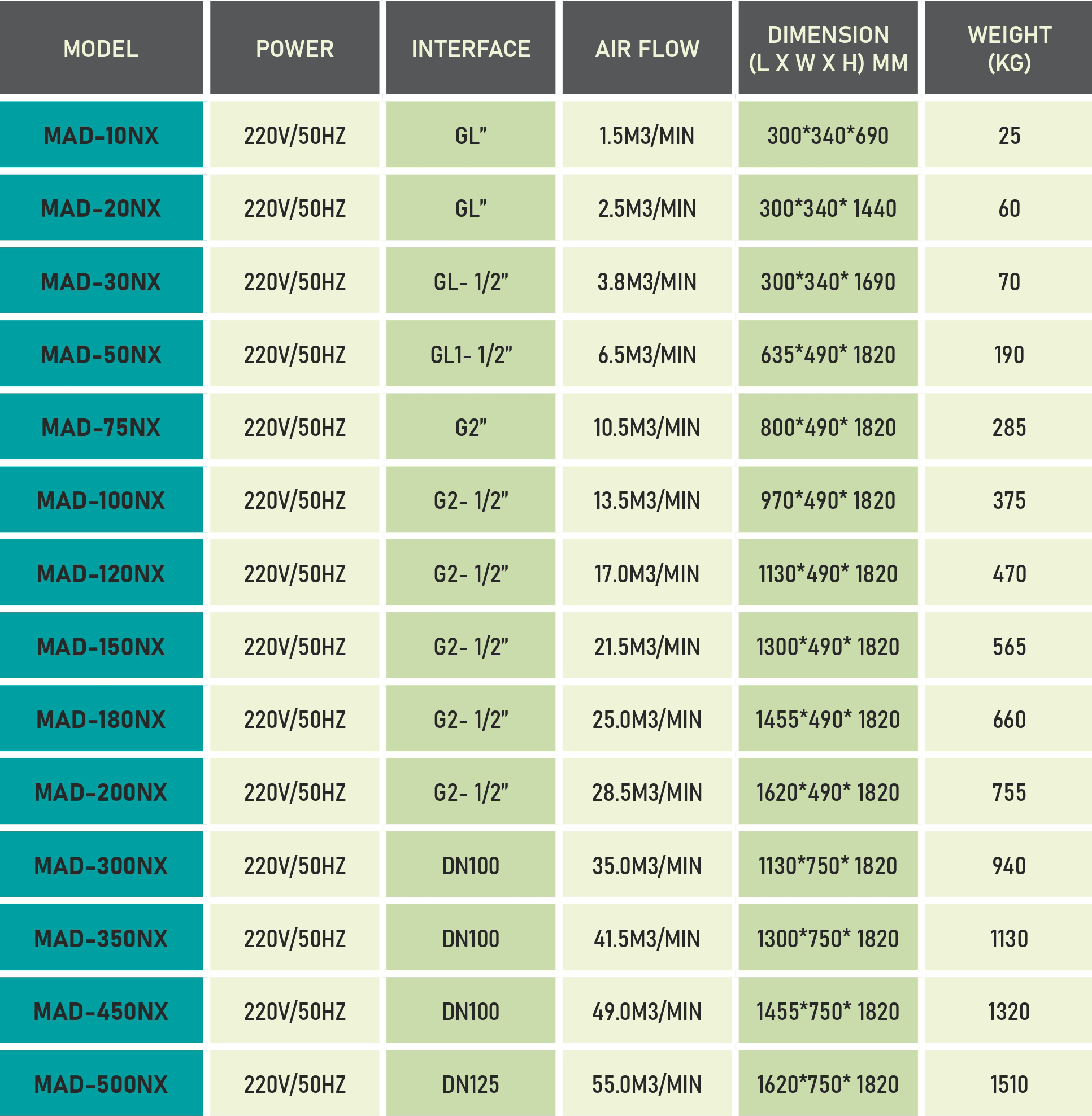